- Insights & events
- Blog
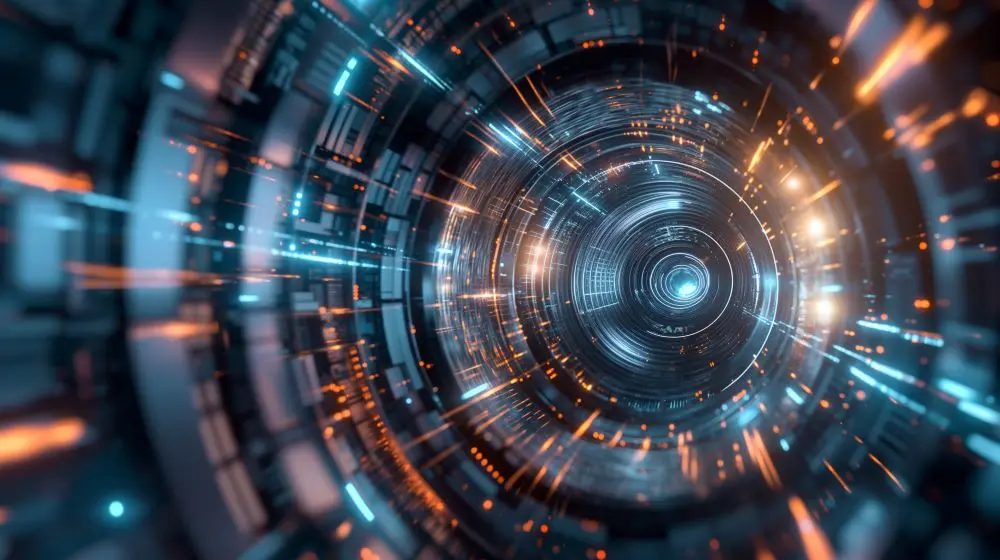
Blog | July 15, 2025
The end of silos: start saving supply chain costs early
How AI-driven optimization boosts efficiency and unlocks supply chain cost reductions
Integrating transportation planning earlier in the supply and material planning process can unlock major cost savings. This approach also helps companies get much more value out of their transportation assets. We’ve seen this across global custonmer projects: bringing transportation into the conversation sooner leads to better logistics performance, without compromising stability or control.
Still, many companies aren’t fully tapping into this potential. Why? In most cases, it comes down to siloed structures and systems that don’t speak the same language.
At 4flow, we’ve developed software that helps overcome this. By aligning material requirements with transportation constraints from the start, we enable AI-driven planning decisions — and it shows. Our customers are seeing clear improvements in cost efficiency, asset utilization, and supply chain agility.
Siloed planning: a costly disconnect
Traditionally, material and supply planners work in silos without collaborating. On one side, supply planners focus on ensuring the continuous availability of components, products, and materials needed for operations. At the same time, transportation planners aim to move goods in the most cost-effective way.
Each team is focused on meeting their own objectives and managing daily disruptions. This leaves little time to explore improvement through cross-functional coordination. Even when individual functions successfully meet their targets, there’s still untapped potential. Supply chain teams can improve efficiency by collaborating and breaking down these silos.
The lack of coordination between planning functions can lead to missed opportunities, inefficiencies, and avoidable costs.
Siloed planning leads to avoidable costs and missed opportunities:
Underfilled trucks
Orders generated without coordination often result in trucks running half-empty, wasting capacity and money.
Last-minute shipments
When orders are made without considering realistic transport schedules, rush shipments can become necessary — driving up costs.
Lost consolidation opportunities
If teams aren’t communicating production and transportation needs, there’s a missed opportunity to combine shipments for greater efficiency.
Reduced agility
Disconnected planning limits a company’s ability to adapt quickly to market changes or supply disruptions.
A new approach: integrating planning for better outcomes
With just one automated step added to the planning process, orders can reflect both operational requirements and transportation constraints from the outset. AI-powered algorithms in integrated planning software process thousands of orders and shipments within seconds – and provide reliable, optimized outcomes.
Here’s how it works: coordinated planning in four steps
The process begins with a material planning run – such as demand planning, replenishment, or supply planning. This generates requirements, orders, or forecasts based on operational needs.
Advanced optimization software analyzes these planned orders or requirements alongside transportation parameters – such as vehicle capacities, consolidation options, delivery periods, and frequency – and identifies optimization potential.
This step adjusts and aligns the plan to:
- Consolidate shipments within a defined, short time horizon (e.g., up to two weeks)
- Improve vehicle utilization by aligning shipment volumes with capacity
The result is a set of optimized orders that already reflect transportation constraints like delivery frequency, capacities and consolidation potential. This provides a reliable basis for downstream processes like transportation planning and shipping. Both supply and transportation planning teams can review these optimized orders and relevant KPIs – this brings transparency across teams and enables alignment and agile decision-making.
Real-time reporting provides visibility into cost savings, resource utilization, and potential inefficiencies. Planners across departments can quickly adapt plans – for instance if demand patterns or market conditions change.
Tangible benefits in action
Our integrated planning approach isn’t just theory – it’s been proven in real-world scenarios. For example, we supported a global automotive OEM that was facing high shipment frequencies and fluctuating demand. The manufacturer saw dramatic improvements when it began coordinating material planning and transportation optimization:
- Fewer shipments, lower costs
By consolidating orders, the automotive manufacturer reduced call-offs from 2,400 to 1,350 over a two-week period. This significantly decreased the number of shipments, resulting in notable cost reductions in transportation and labor. - Enhanced reliability
With transportation constraints already reflected in orders, the manufacturer boosted efficiency in material planning and enabled stable delivery processes. - Quick time-to-value
In just a short 6-month pilot phase, targeted optimization across material and transportation processes helped the manufacturer achieve measurable cost savings and greater supply stability.
After integrating early-stage transportation optimization into material planning the software 4flow TORO runs daily to optimize 1000 supplier relations and over 25,000 scheduled lines for the manufacturer. Shipment utilization increased by 74%. The manufacturer also saw a transportation cost reduction of 17%, and the overall efficiency of the supply chain significantly improved.
4flow TORO offers a practical solution to the challenges posed by supply chain silos. By integrating material and transportation planning, organizations can achieve substantial cost savings and improve their supply chain agility.
Our team collaborates closely with customers to understand their specific needs and implement solutions that drive real, measurable improvements. The business case is clear, and long-term the competitive advantage is significant. It's time to take action and realize the full potential of your supply chain.
Ready to see how aligning your planning processes can make a real difference?
Contact us to learn more about 4flow TORO.
Author
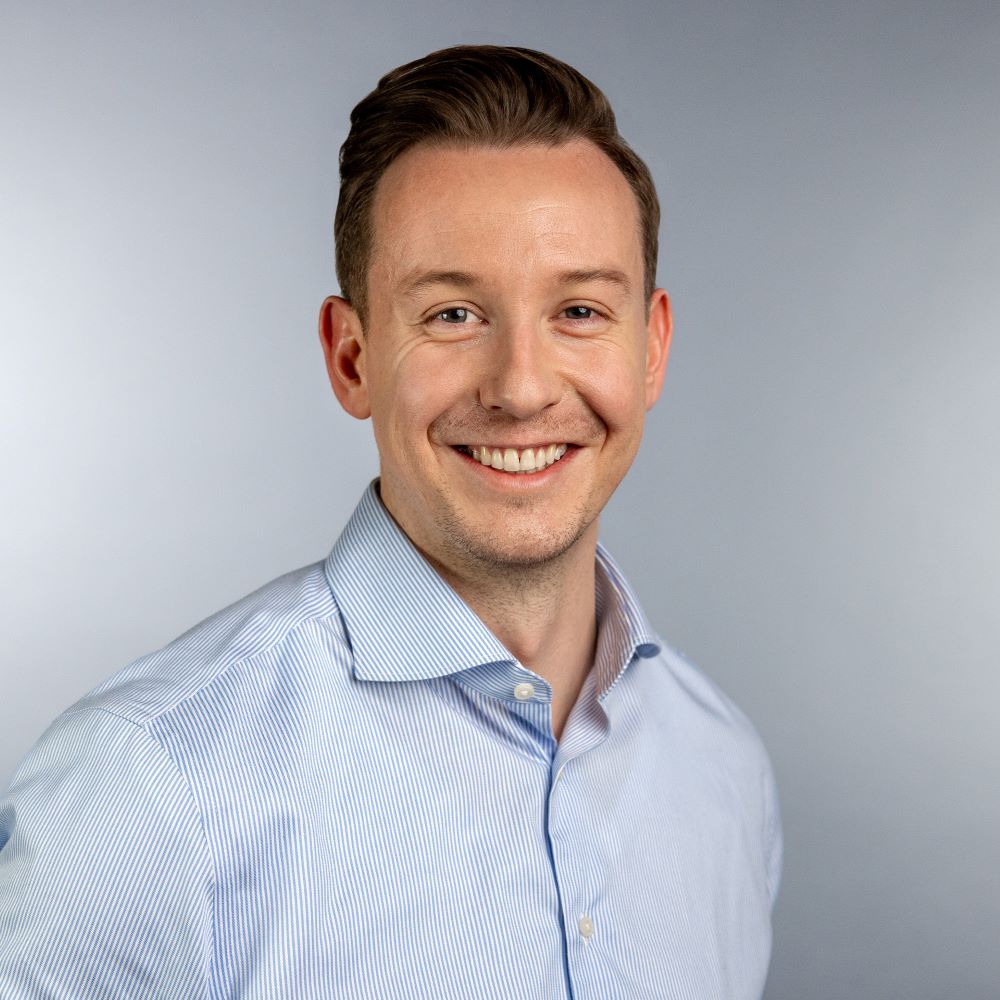
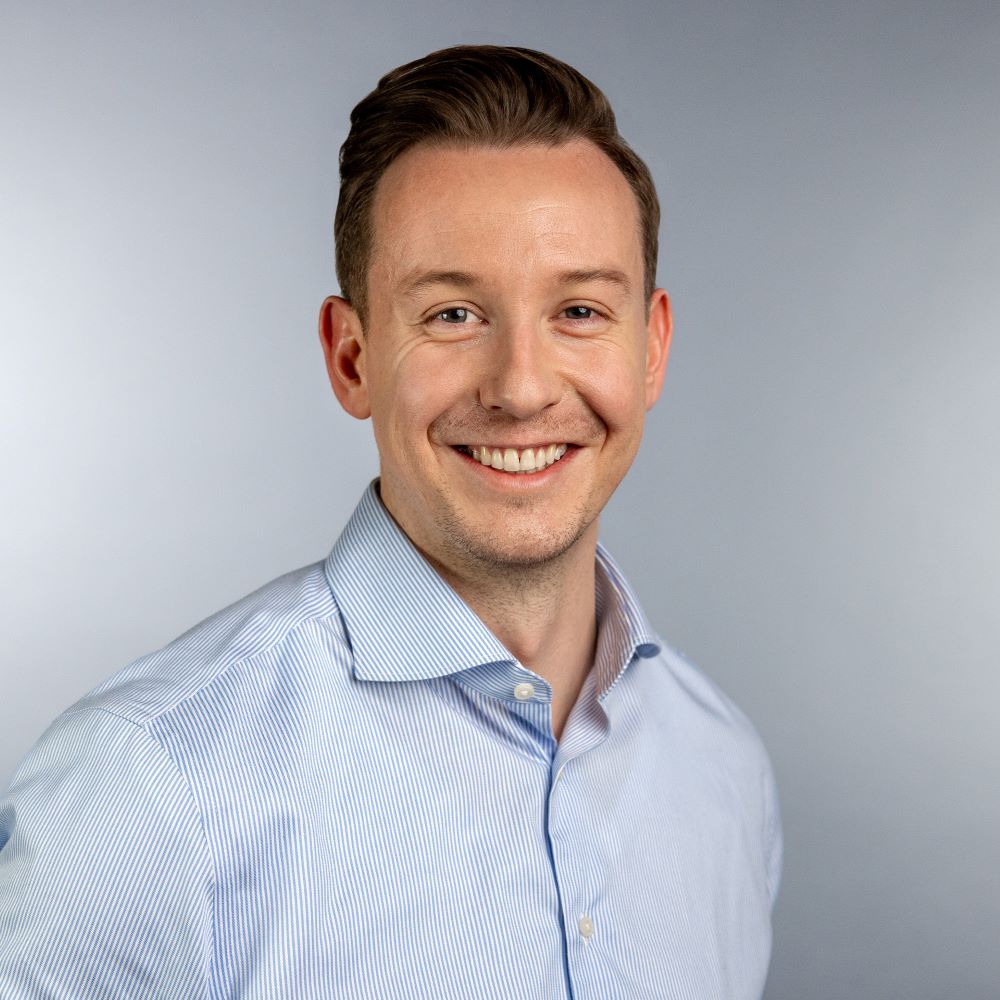
Patrick Achatz
Director Software Sales
4flow software