-
Shaping the futureof supply chain
-
A new era of international trade
-
Supply chain orchestration
-
Success story Thalia
-
Selected success stories
ExploreTrusted by industry leaders
As an innovative partner, we collaborate with our customers to develop solutions for the future.
Contact us
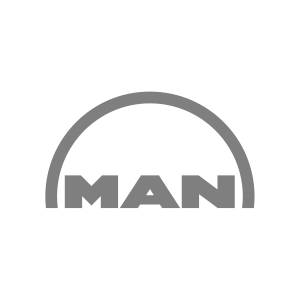
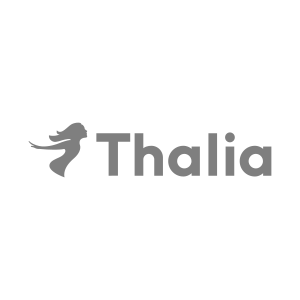
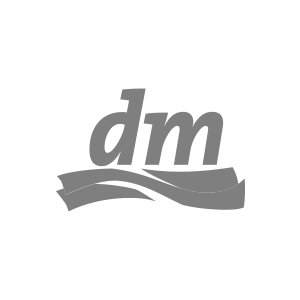
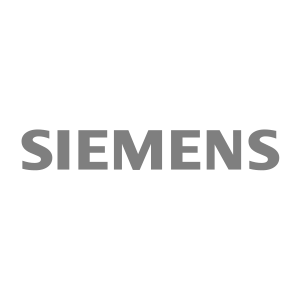
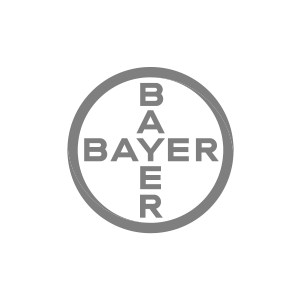
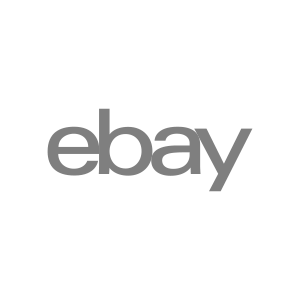
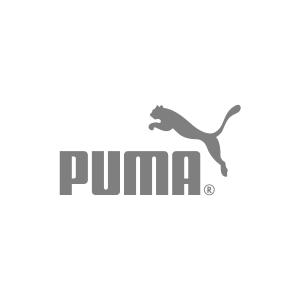
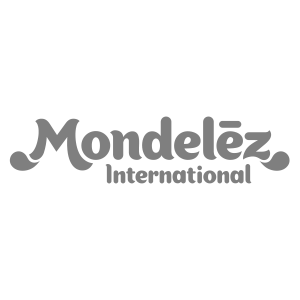
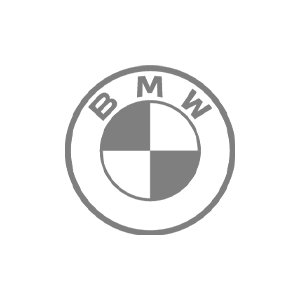
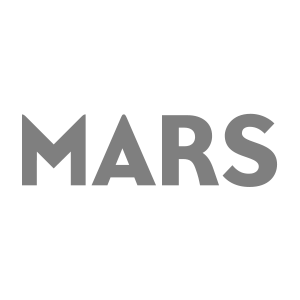
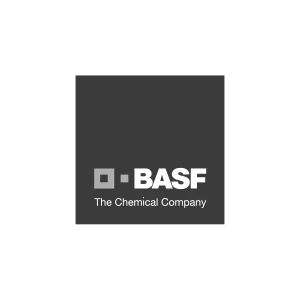
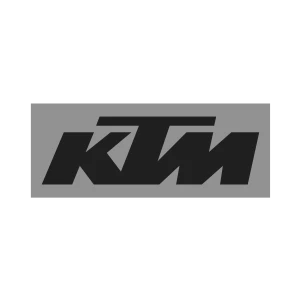
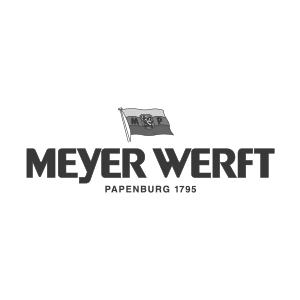
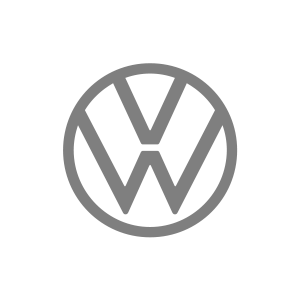
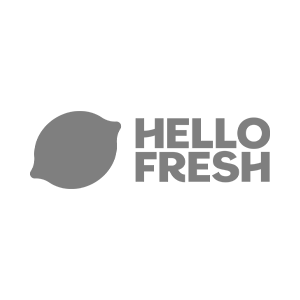
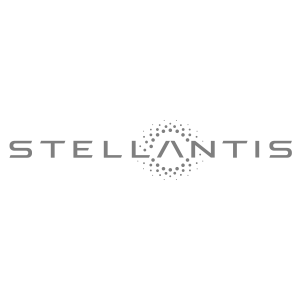
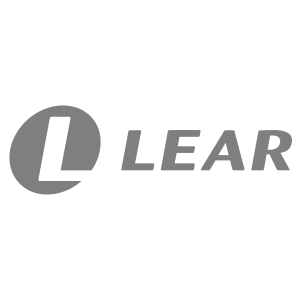
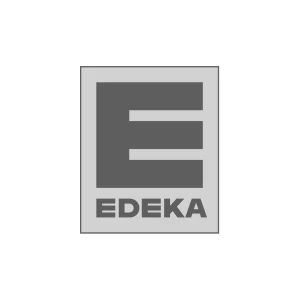
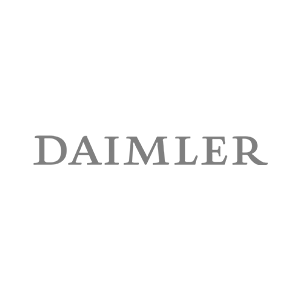
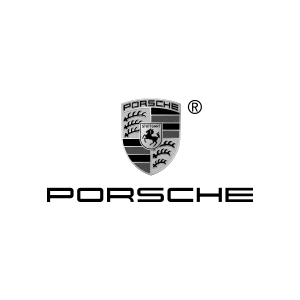
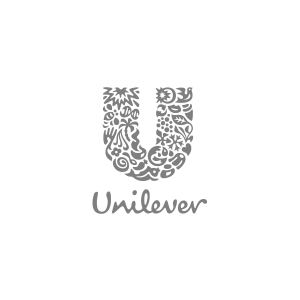
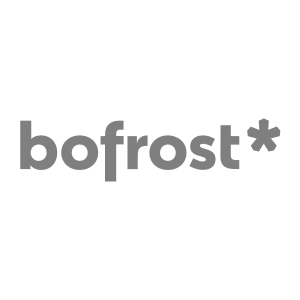
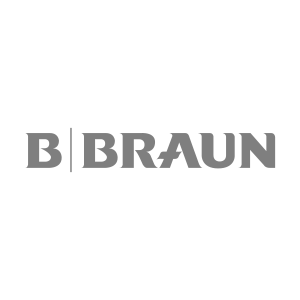
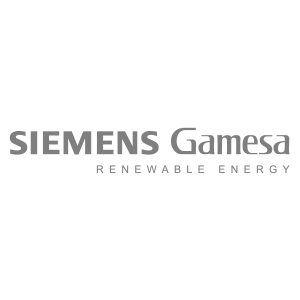
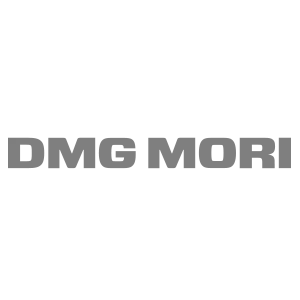
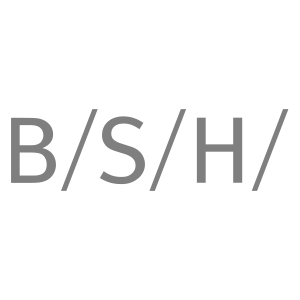
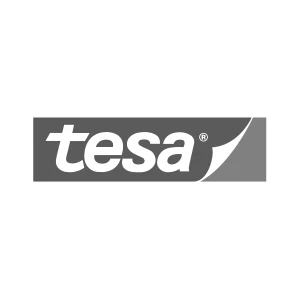
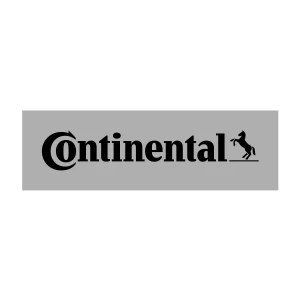
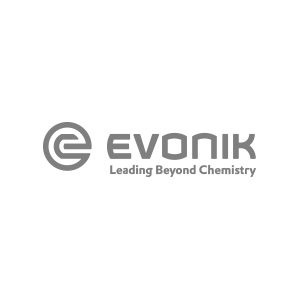
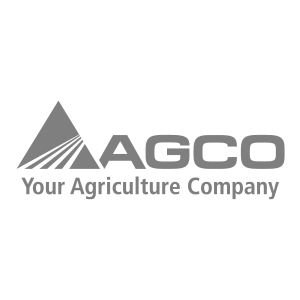
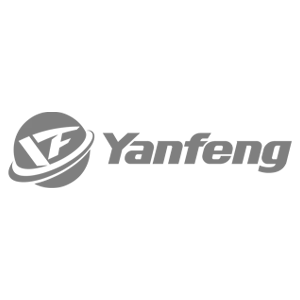
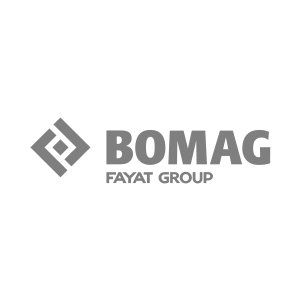
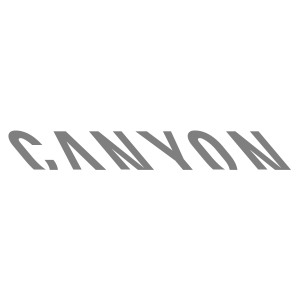
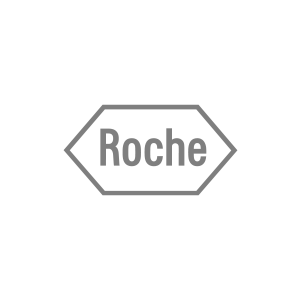
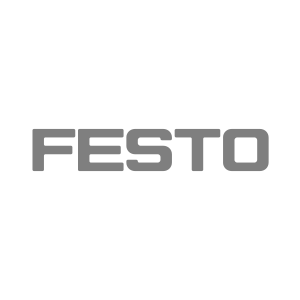
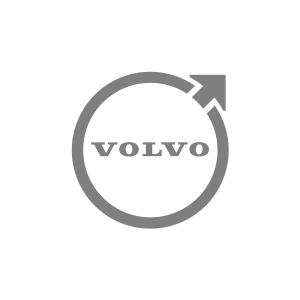
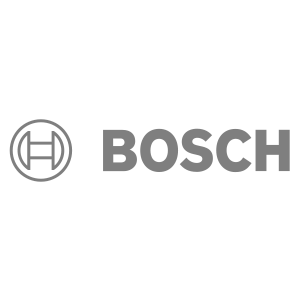
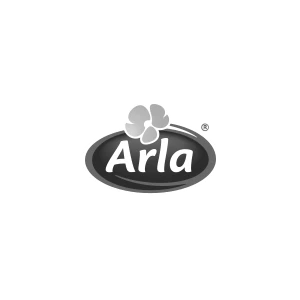
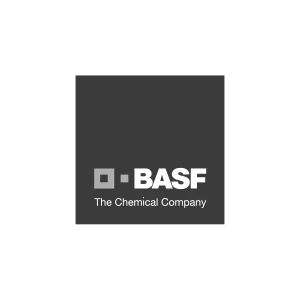
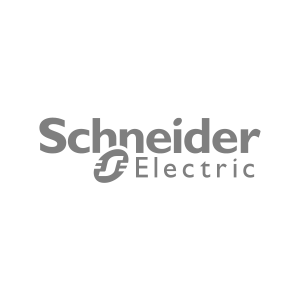
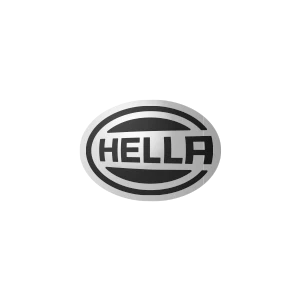
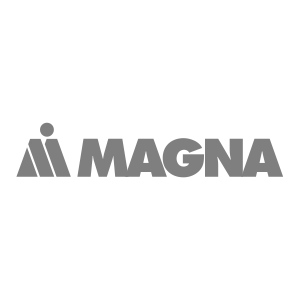
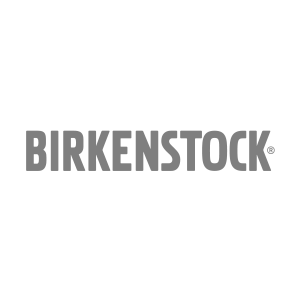
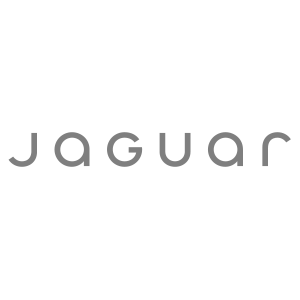
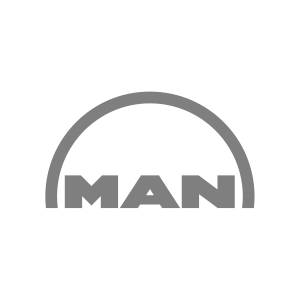
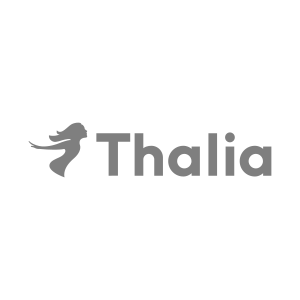
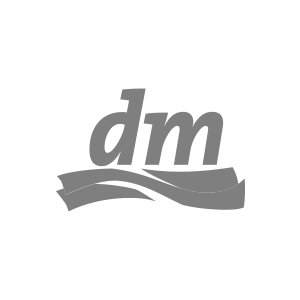
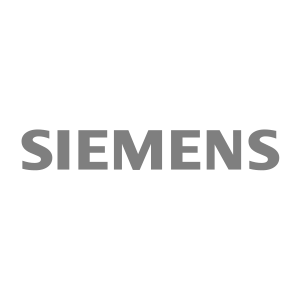
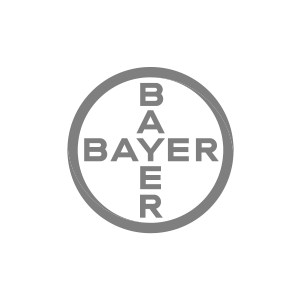
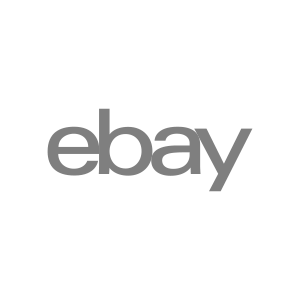
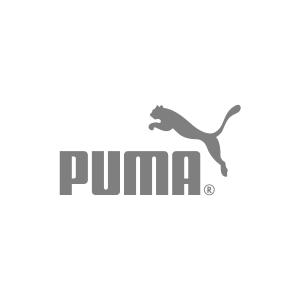
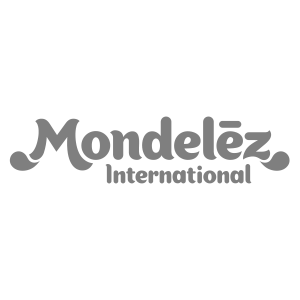
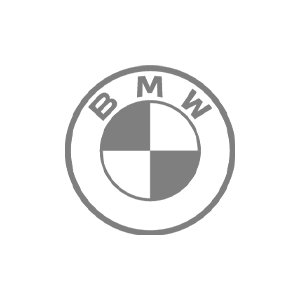
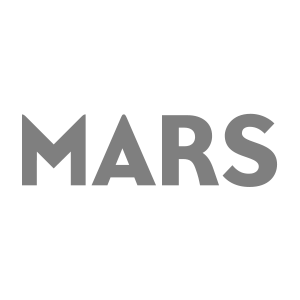
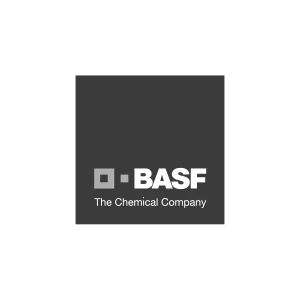
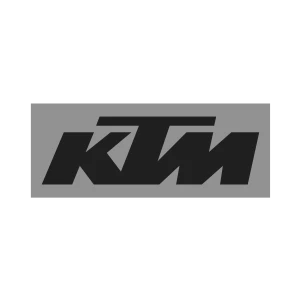
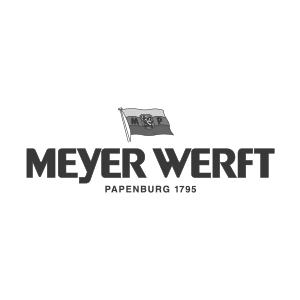
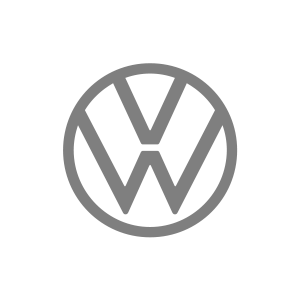
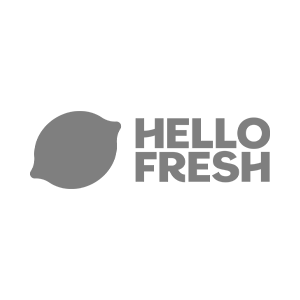
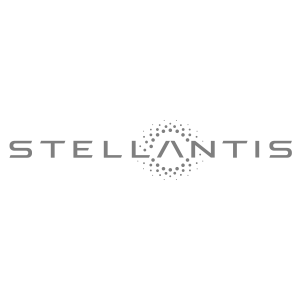
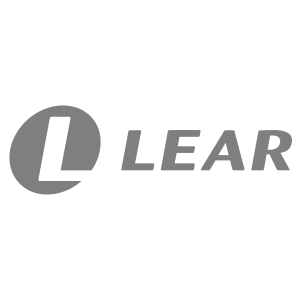
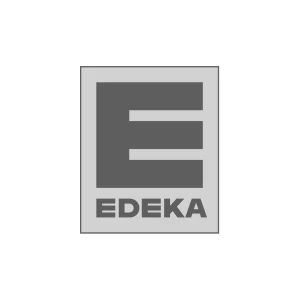
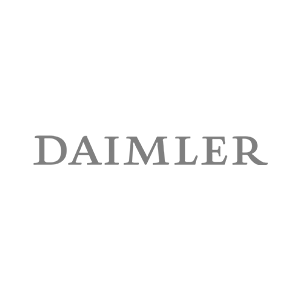
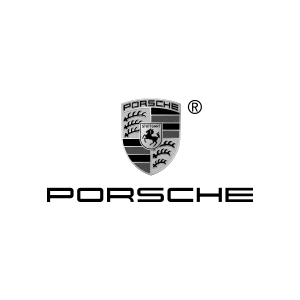
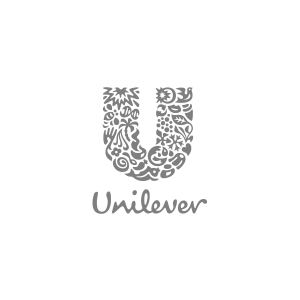
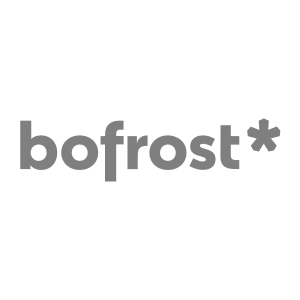
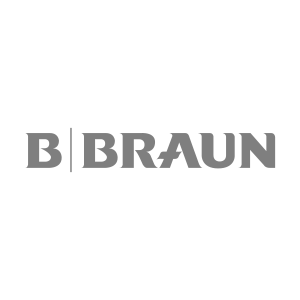
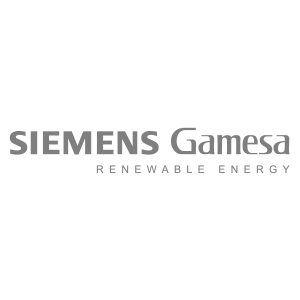
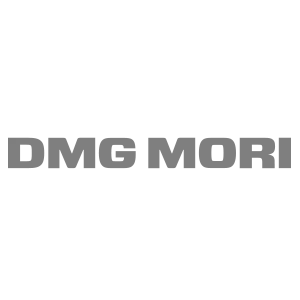
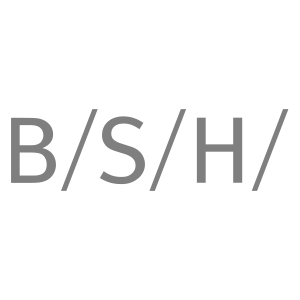
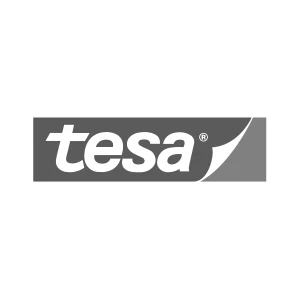
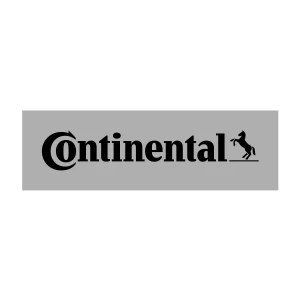
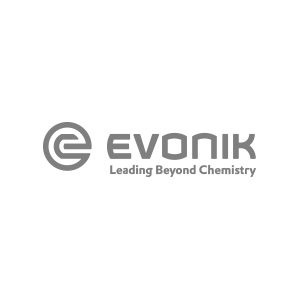
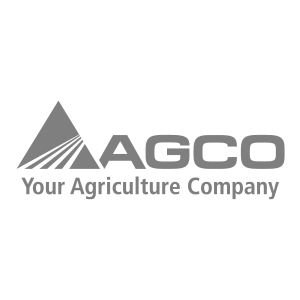
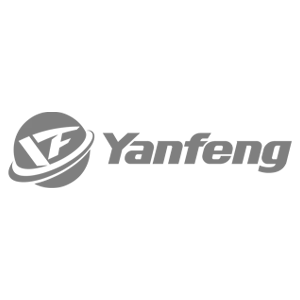
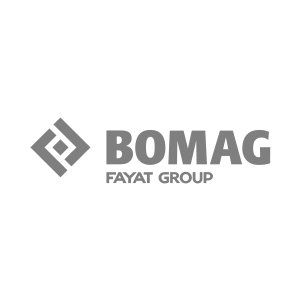
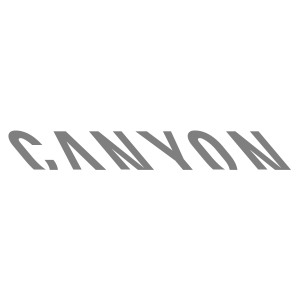
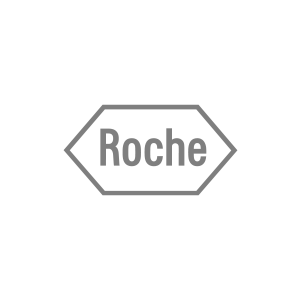
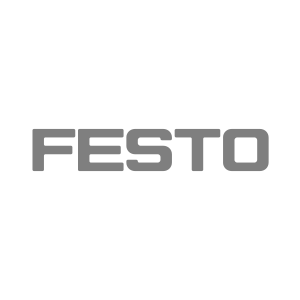
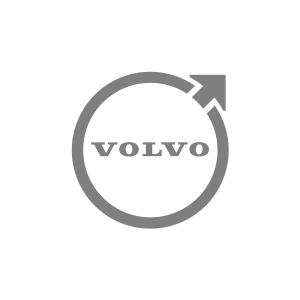
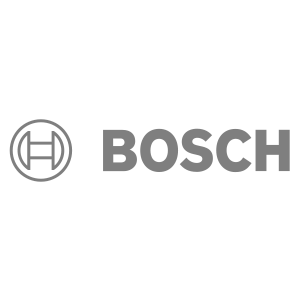
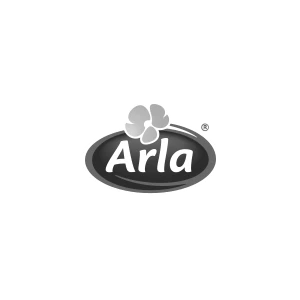
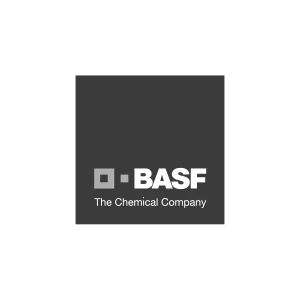
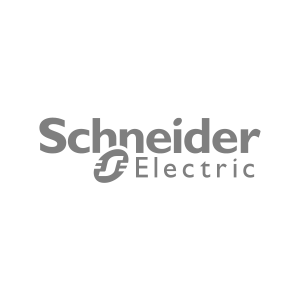
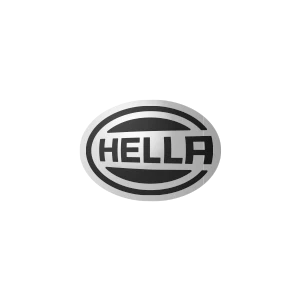
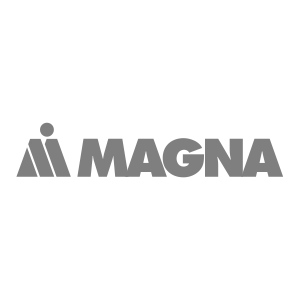
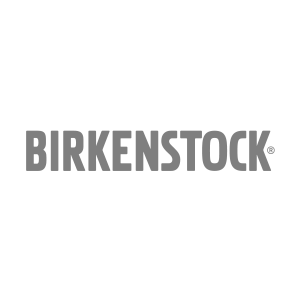
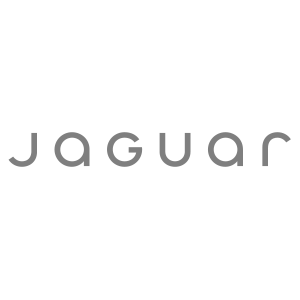
20+ locations globally
With offices in North and South America, Europe and China, we are where our customers are. Our footprint lets us work closely and hands-on with global supply chains.
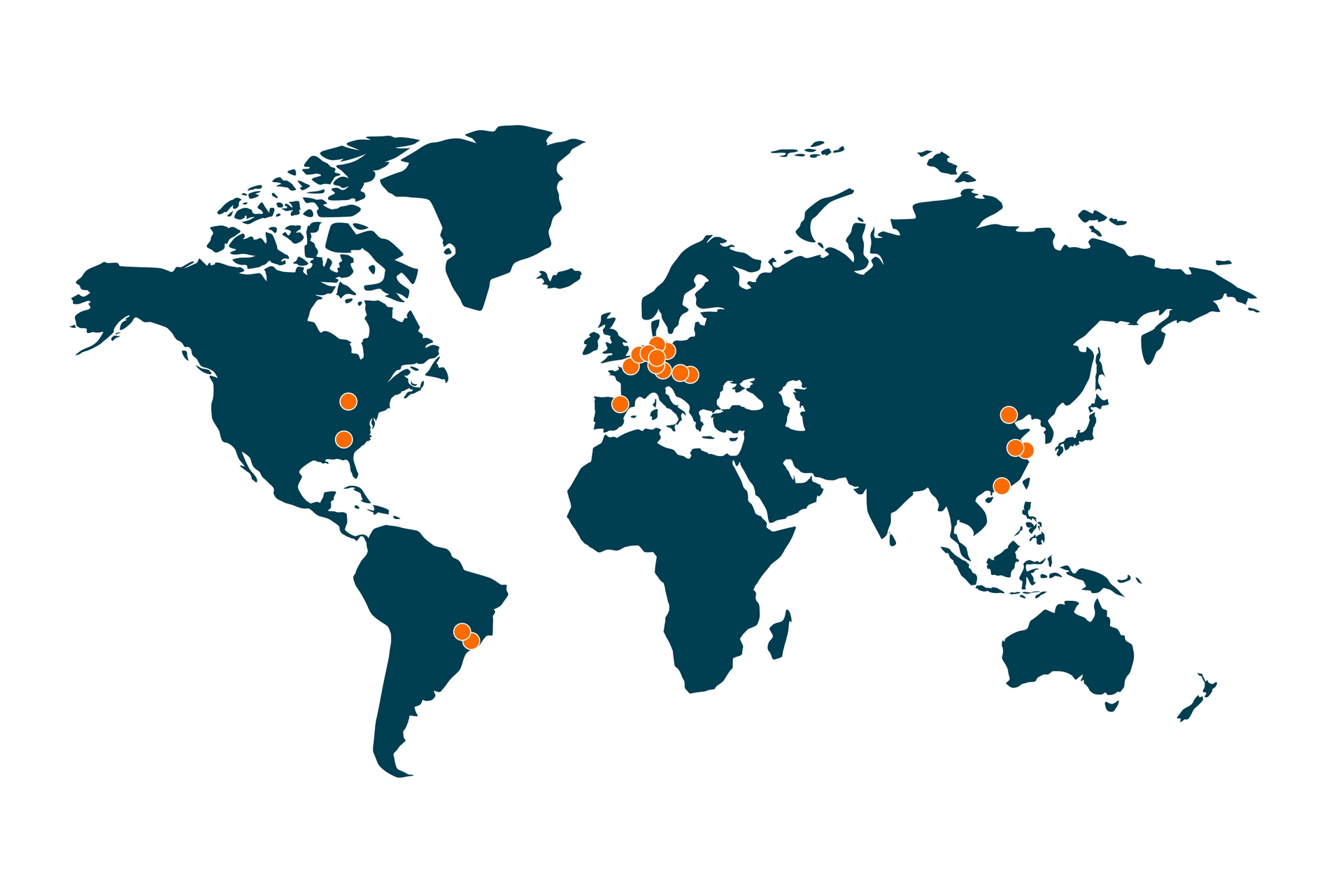
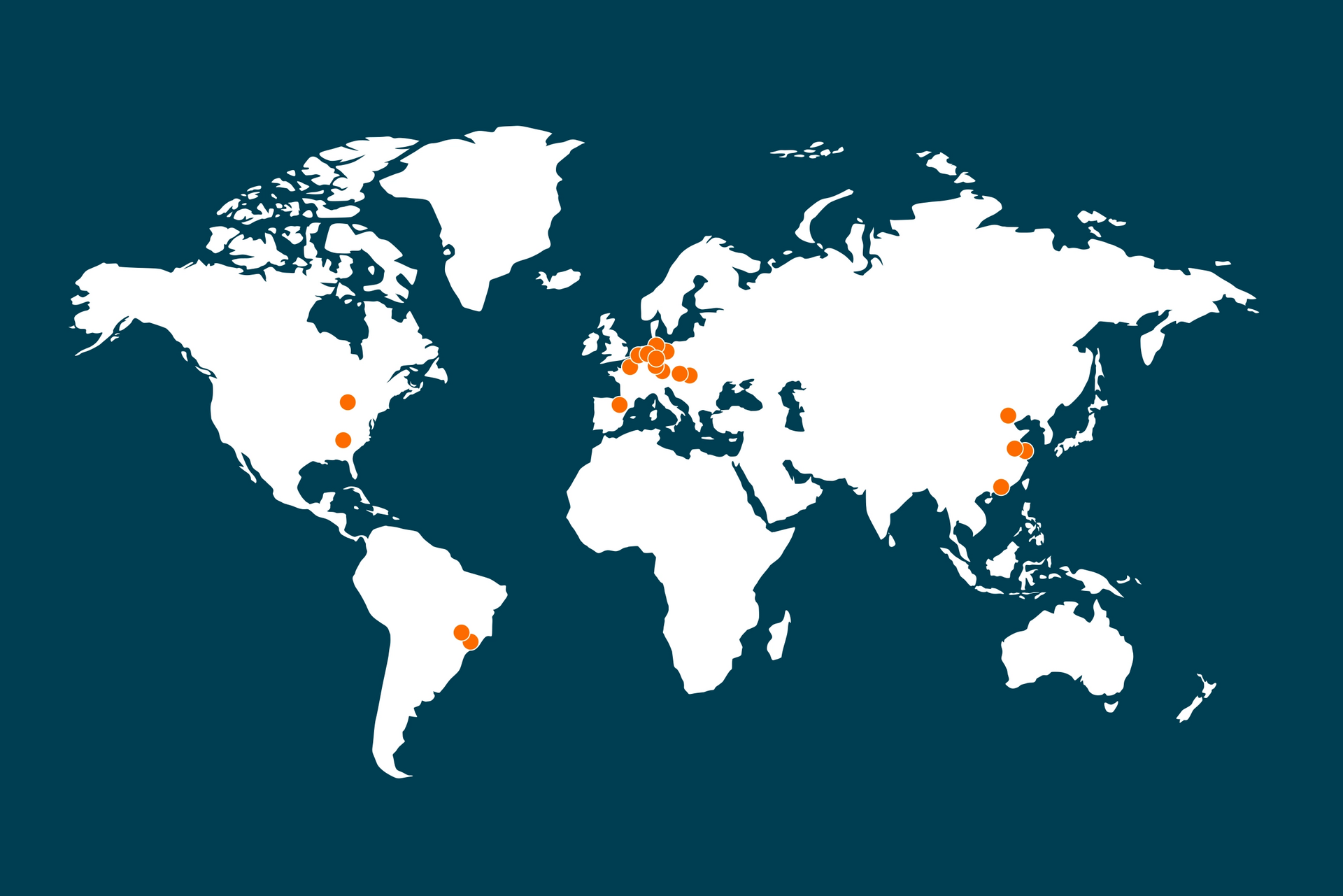
Events
Upcoming events
On-demand webinars
On-demand webinars
What's new?
ExploreReady to optimize your supply chain?
As an innovative partner, we collaborate with our customers to develop solutions for the future.