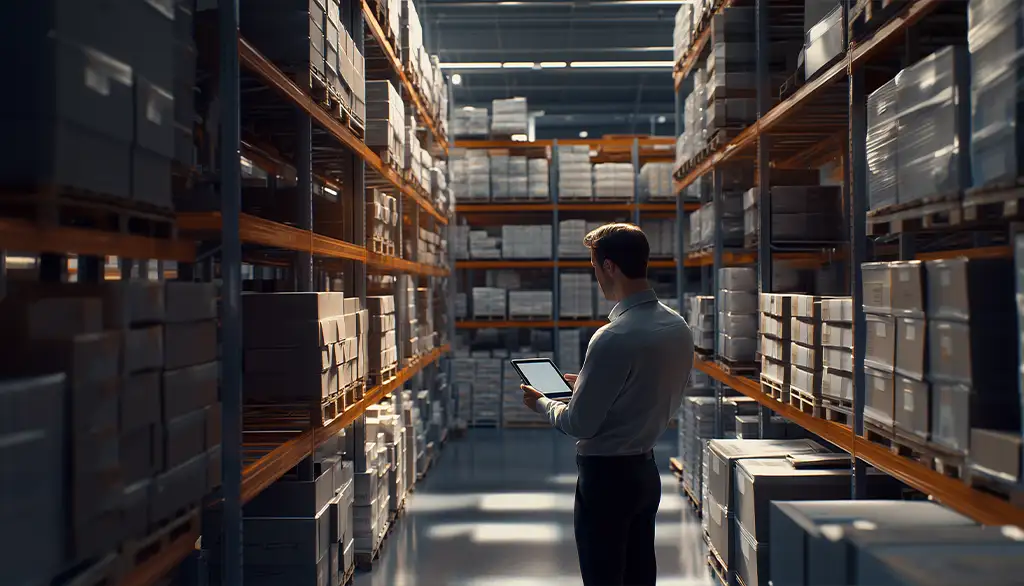
- Consulting
- Supply chain planning & optimization
- Fulfillment and distribution
Optimize, connect and digitize your fulfillment and distribution
Design and implement new distribution centers and navigate your smart warehouse transformation
Achieve process optimization and sustainable cost reduction
- Benefit from end-to-end-support and task force management
How can you successfully implement digital transformation to prepare your fulfillment and distribution network for the future? How can you reduce costs while increasing efficiency?
4flow supports you in to establish new logistics locations, enhance existing distribution centers and transition them to smart warehouses. From strategic planning and process optimization to digital transformation, we provide tailored solutions to meet your business needs.
How we optimize your fulfillment and distribution centers
Distribution center design and implementation
Implementing a new logistics site is a complex transformation project. It requires effective and efficient collaboration between all stakeholders. With over 20 years of experience, 4flow supports you through each step of your distribution center transformation: from strategic planning through tendering and equipment procurement to go-live.
4flow also handles the central project management to coordinate between stakeholders such as logistics, construction, IT and human resources. In this role, we ensure all relevant functions are considered in both planning and implementation.
Smart warehouse, automation and robotics
Autonomous internal transport systems, robotics for material handling, AI-driven demand forecasting and flexible warehouse automation are setting new standards in warehouses. In many organizations, these solutions – especially robotics – are often implemented in isolation. Even businesses with advanced digital capabilities frequently leave untapped potential by not fully integrating smart technologies and information flows across their warehouse operations.
We work closely with your team to assess your current state and identify the best path toward a truly smart warehouse. We help you develop a clear vision and an actionable roadmap, tailored to your needs and priorities.
Our approach covers:
- Seamless integration of IT systems
- Implementation of state-of-the-art automation and robotics solutions
- Utilization of advanced identification technologies
- Optimization of digital management and data processing using business analytics platforms throughout your process chain
We help you connect, automate and digitize your logistics – from strategy to implementation – so your warehouse is ready for the future.
A smart warehouse with connected processes
Distribution center cost and performance optimization
4flow delivers efficient solutions to optimize your distribution centers for today and tomorrow. We analyze your current processes and infrastructure, align them with your growth plans and identify the ideal setup for your needs. With targeted adjustments to processes, layouts and material flows, we help you unlock cost savings and boost efficiency.
Our experts also support you to evaluate investments and implement measures that ensure long-term improvements. Through scenario analysis and sensitivity checks, we make sure your distribution center remains resilient and flexible – even as volumes or product mixes change.
The result: cost- and space-optimized distribution centers, ready for the future.
Task force management
Unexpected bottlenecks, inefficient processes and high inventory levels can quickly disrupt your operations and drive up costs. When transparency is limited and processes are poorly coordinated, these challenges become even more difficult to manage. Rigid or poorly integrated IT systems can further complicate matters, making it harder to respond quickly and effectively.
In today’s fast-paced environment, businesses need solutions that deliver results – without interrupting ongoing operations. With structured task force management, 4flow helps you quickly identify and address vulnerabilities in your processes. Our experts analyze the root causes of bottlenecks and inefficiencies, then work side by side with your team to implement targeted improvements for immediate impact.
Sound interesting?
Contact usThe benefits of your future-ready fulfillment and distribution with 4flow
-
Smart warehouse transformation
Integration of automation, robotics and IT systems for a future-ready warehouse.
-
Resilience and flexibility
Scenario analysis ensures your distribution center adapts to change and remains robust.
-
Cost reduction and efficiency
Targeted process improvements deliver measurable cost savings and greater efficiency.
-
End-to-end support
Comprehensive guidance for planning, optimizing and digitizing new or existing distribution centers.
-
Rapid problem solving
Task force management quickly identifies and resolves operational bottlenecks.
-
Global team at your side
Leverage 4flow’s over 100 intralogistics and production experts for your project.
What our customers say
Proven success with top businesses
- Infineon
- CCC
- HelloFresh
- JOST