- Insights & events
- Success stories
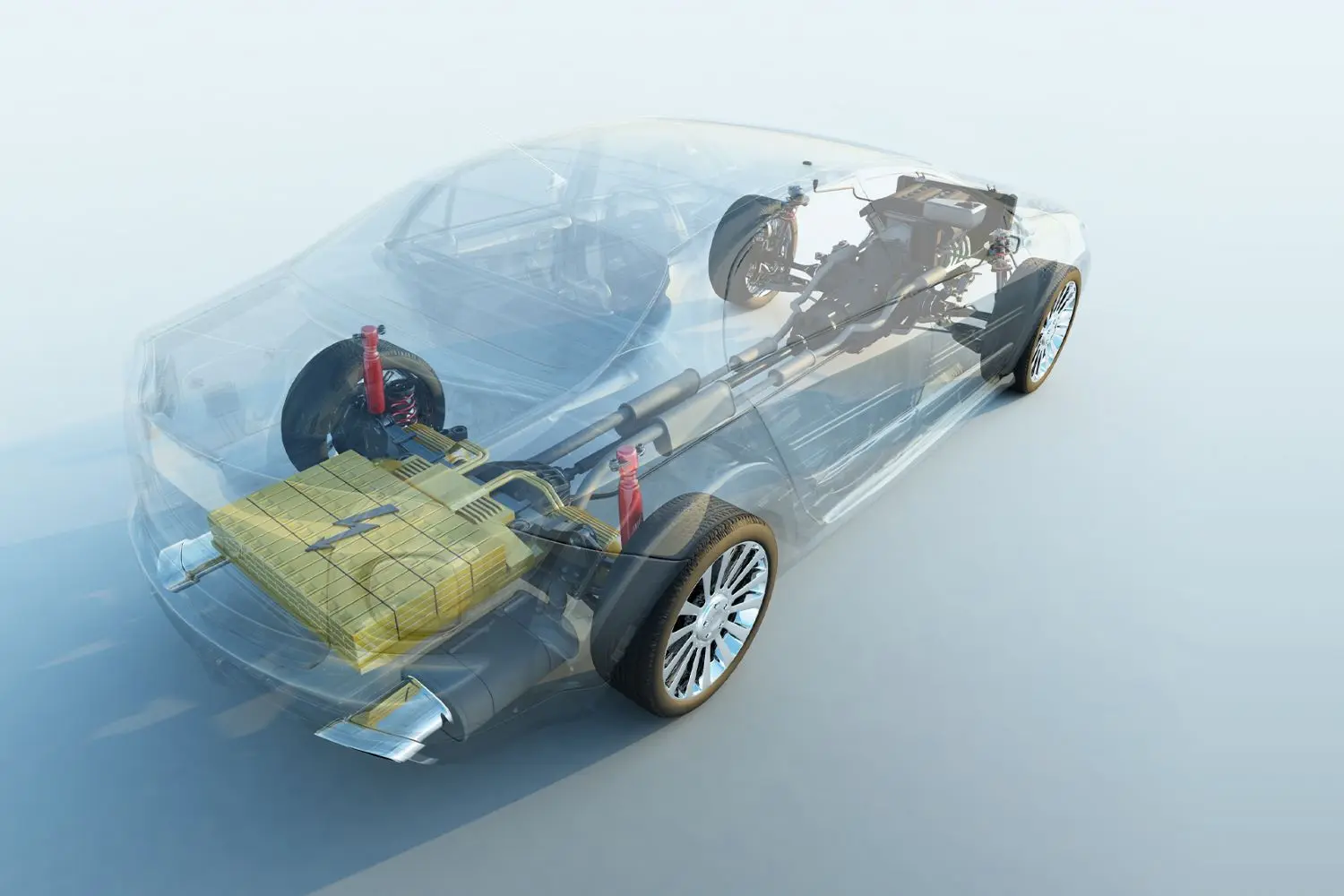
Automotive manufacturers
Success story
Mercedes-Benz
4flow plans a powertrain plant’s supply chain transformation to electric mobility
Around the world, vehicle manufacturers are faced with the challenge of ensuring the smooth and efficient transformation from conventional drive systems to new ones. The plant of Mercedes-Benz AG in Hamburg, Germany, is an important element in the powertrain production network and a high-tech location for electric mobility drive components. 4flow supported the plant in preparing a series of transitions characterized by high variance in products and materials along with many new processes. In order to ensure a smooth transformation, the supply chain was designed with maximum flexibility in mind.
With 4flow as partner from strategy to implementation
Thorough preparation for the complete transformation to electric mobility during routine operations is vital. It starts with answering a series of important questions. How can supply chain manage a transformation within existing plant and building structures? How is it possible to manage supply to the production and assembly areas in a way that is both future-oriented and cost-efficient? For optimal benefits, managers at the powertrain plant worked together with 4flow on specific projects, ranging from strategy development to the detailed planning and implementation of processes and layouts.
What resulted were optimal building layouts based on brownfield for the year 2021 and beyond, including directed material flows even in areas with very limited space. New supply and management concepts were also designed. The strategy that was developed now serves as a foundation for all supply chain and production planning.
Optimizing and scheduling material flows proactively
In order to implement the strategies, the vehicle manufacturer and 4flow developed roadmaps to create transparency on milestones for production and plant planning, IT and supply chain. Especially critical aspects of the roadmap were highlighted in detail using deep dives. As a result, impending bottlenecks in the supply chain were identified at an early stage, and countermeasures were proactively defined.
One example for this is material supply planning and the associated production scheduling for buffer planning between processing steps for the production and assembly building. Due to the increasing number of new series expected in the future, this is an area expected to cope with an enormous increase in product variance. 4flow quantified space restrictions by analyzing comprehensive quantity frameworks, which consider from among existing and future bill of materials lists, container concepts, sales figures and setup concepts. Based on this transparency, the vehicle manufacturer and 4flow were able to develop an optimized scheduling process at an early stage, which accounted for an increase in variance and quantity in the unchanged building areas. This resulted in avoiding large investments.
Another example is space- and process- optimized material flow planning of the assembly line. With axles for electric vehicles and conventional vehicles produced on a single line, high demand is placed on the production and supply chain concept. Together with 4flow, supply chain planning at the plant of Mercedes-Benz AG in Hamburg developed ideas to tackle this complexity. In order to avoid bottlenecks, optimal supply to the line was implemented according to the line-back principle. When put together with cart and set concepts, a high level of flexibility is guaranteed.
Well-proven methods in use
4flow applied proven standard methods in all project phases from strategy to implementation, which were then adapted according to respective objectives and premises. Layout and material flow planning software is used, for example, to visualize different layout scenarios in either 2D or 3D in real time.
Developing successful concepts for space, material flow and production scheduling was heavily dependent on the intradepartmental cooperation of supply chain planning, production scheduling, material management and IT in all project phases. As a neutral player, 4flow’s role in finding the right processes served to facilitate an optimal comprehensive solution. “If all stakeholders are convinced of the procedures and solutions and learn from one another, then the solutions will be implemented and applied for the long term,” said Ralph Eberspaecher. In this regard, 4flow also stands to benefit from the wealth of experience in handling such projects.
Sounds interesting?
Contact usTestimonials
At a glance
Customer: Mercedes-Benz
- 2,400 employees in Hamburg, Germany
Project scope:
- Plan the transformation of a powertrain plant from conventional to new drive systems – from strategy development to detailed planning – and implement processes and layouts.
Results:
- Early identification of bottlenecks in the supply chain
- Development of an optimized production scheduling process for visualizing increases in variance and quantities at plant areas that remain unchanged
- Space and process optimized material flow planning of assembly line
- Avoiding unnecessary, large investments